Project report: BrandSafway’s work in NYC
06 February 2024
AECOM Tishman contracted with SafwayAtlantic to design, supply, install and dismantle a six-car construction hoist complex for Two Manhattan West.
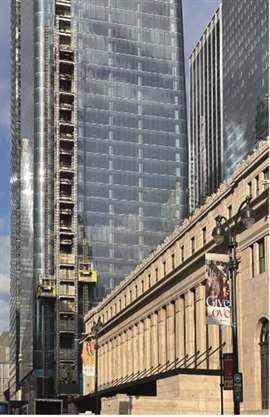
Two Manhattan West was designed by Skidmore, Owings & Merrill (SOM), developed by Brookfield Properties and the general contractor is AECOM Tishman.
Scaffold & Access Industry Association Project Award WinnerBrandSafway won the 2023 Scaffold & Access Industry Association’s Mast Driven Platforms Project of the Year Award for its work on Two Manhattan West. This Association’s Mast Driven Platforms Project of the Year Award is presented to a member company where mast driven hoists and platforms were utilized to:
For more on the SAIA Project Awards, visit www.saiaonline.org. |
SOM describes the project as “one of the largest and most complex developments underway in New York City. The project, bound by Ninth and Tenth Avenues and West 31st and West 33rd Streets, is part of the larger revitalization of Manhattan’s rapidly changing Far West Side.”
The two-million-square-foot tower, which aims for LEED Gold status, is clad in high-performance glass that accentuates an elegant simplicity in the reflected the sky. The chosen access solution would pay a major role for efficiently installing 8,100 curtain walls, which are aluminum frames containing the high-performance glass that form the non-structural outer covering of the building.
BrandSafway’s common hoist tower design helped the contractor solve a major structural engineering challenge with ground loading issues. The solution also minimized traffic disruptions and sidewalk closures and enabled an efficient construction pace for transporting the 8,100 curtain walls and approximately 650 construction personnel.
Ground Loading Issues
Two Manhattan West stands on an extremely challenging site above active rail lines. Navigating this challenge required an intricate synthesis of design and engineering. Each tower is supported by a central core with sloping perimeter columns that reach available foundations around the trains. At Two Manhattan West, only half of the core could touch down to solid ground. The architect aligned sculpted mega-columns at the building’s perimeter with subgrade spaces between the tracks.
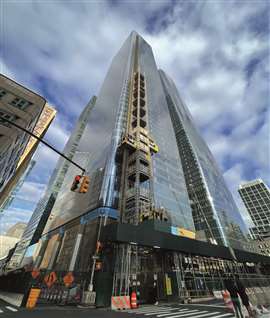
On a construction site with firm bedrock, the hoist complex would rest on pads or steel plates on top of the sidewalk or road. However, in addition to the trains, a basement underneath the building further complicated load placement — and the hoist complex has a load of 266,000 pounds. Fortunately, the building had a steel framed plaza. Working with the building engineer, BrandSafway designed dunnage steel (a supporting structure for the hoist complex) so that it would transfer the load to the building steel.
Tight Quarters
The common tower is made from shoring and scaffolding components decked at each entry level to allow exit of the hoists and access to the building under construction. Each of the four tower legs and secondary mast hoist use industry standard 650 x 650 mm square mast sections constructed of high tensile steel and fabricated in 1500 mm-tall sections. To secure the mast hoist to the common tower, hoist ties were welded to the common tower steel frame and bolted to the mast tower.
The hoist complex needed to fit in a very limited space. To create clearance at ground level, the mast hoist for cars C and D actually starts on the second floor. BrandSafway designed a structural frame from 12 x 12 x ½-in. tube steel topped with a W30 x 148 I-Beam that tied into the building’s steel frame and the base dunnage. Cantilevered approximately 8 ft. past the common tower frame, this structure provided a base for the mast hoist for cars C and D, supporting a load of approximately 130,000 pounds.
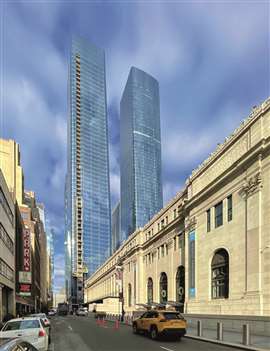
The ingenuity of this unconventional design demonstrates how access providers, working with building engineers, can improve construction efficiency. In this case, cars C and D created additional capacity to move personnel, who entered the cars via a set of stairs from the ground floor.
Efficiency
New York City construction practices set efficiency standards from which others can learn. Elsewhere around the world, mast hoists would tie directly to the building. Conversely, BrandSafway and general contractors such as AECOM Tishman use common platform to create a hoist complex.
Instead of requiring three masts (each with dual-car hoists) tying into the building — each of which would require its own set of tie-ins —BrandSafway’s design created a six-car hoist complex that has a single set of tie-ins at each level.
Typically, hoist cars for New York City projects are rated for 7,000 pounds, but the six cars were rated for 8,000 pounds because of the length required to fit the curtain walls. As architects design higher ceilings that require taller curtain walls, access has evolved to meet their needs.
Using fewer ties minimized curtain wall “leave-out,” which is the amount of curtain walls that must remain uninstalled during erection. Instead of 10 curtain walls leave outs for six cars, the BrandSafway design limits leave-out to just three curtain walls. As a result, the contractor can close up the building faster and move it closer to occupancy. A smaller leave-out also keeps out more of the elements during construction.
In addition to the six hoist cars, SafwayAtlantic also equipped the hoist complex with a Hydro Mobile mast climber. Affixed to the outer masts of the common tower and positioned above the hoist cars, the mast car also moved up and down the tower with a rack-and-pinion system.
MAGAZINE
NEWSLETTER
The gold standard in market research
Off-Highway Research offers a library of more than 200 regularly updated reports, providing forensic detail on key aspects of the construction equipment industry.
Our detailed insights and expert analyses are used by over 500 of the world’s largest and most successful suppliers, manufacturers and distributers, to inform their strategic plans and deliver profitable growth.