Beyond telematics: How Trackunit is changing the industry
22 August 2023
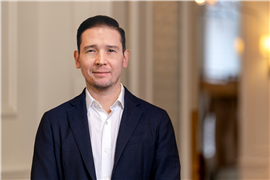
It’s been nearly two years since Trackunit acquired the Industrial IoT division of its then-competitor ZTR. The deal, which created a single business unit between the two tech-forward giants, also marked the starting point of what has been ongoing, significant change within the construction industry’s telematics landscape.
Led by CEO Soeren Brogaard, Trackunit set out to accelerate the digital transformation of construction, an ambitious goal, yet one that the company has diligently – and successfully – chipped away at.
In June alone the company rolled out a number of new solutions for the industry: Marketplace, which allows managers of mixed fleets to access aggregated data sources that have been harmonized and standardized and; Sites, which is software used to monitor, plan and report jobsite needs and fleet allocation accordingly.
The company also recently turned its attention to the evolution of Access Control, which it says is advancing from its origins of simply registering who can and cannot be on a jobsite, to potentially guarding access to all types of machinery, dependent on the qualifications of any given person.
While Trackunit has paced its debuts strategically – launching new solutions separately instead of within one fell swoop – the announcements and timing are all a part of a bigger picture, says David Swan, senior vice president of products for the company.
“In 2023, we are going to launch a series of capabilities in software and hardware that are going to support each other,” Swan told ALH earlier this year. “The idea is that when you look at efficiency, profitability and productivity, it’s always about the jobsite, the rental yard and the OEM logistics yard.
“They want to be able to naturally track things based on their geographical location, not just a list of machines. We’ve heard that a lot from rental companies, that they want to look at a single branch or all their branches and they want to understand when things are coming or going, when they return or leave, and are they on or off rent.”
Simply put, Swan says, it’s a different way to look at connectivity.
Developments in developing
One of Trackunit’s latest launches is Marketplace, a solution that will “transform fleet owners’ data-feed experience,” according to the company.

“Marketplace will allow mixed-fleet owners to easily access aggregated data sources that have been harmonized and standardized,” says Lærke Ullerup, chief product and marketing officer. “This will enable them to streamline their internal business processes with significant downtime implications, freeing up resources for other things.
“Mixed-fleet owners no longer need to spend time, money, and process on putting together big teams as they can significantly reduce time and effort spent collecting and aggregating the data,” she said. “Effectively, they choose what they need from the Iris ecosystem through a self-serve automated approach.”
At its core, Ullerup notes, Marketplace is about enabling mixed-fleet service providers to cope with the increasing complexities of modern construction.
Marketplace is being introduced to the industry in phases; additionally, it will soon enable partners and external developers to build market-facing apps or data connectors for customers leveraging Iris’s data-led insights engine. Developers will be able to build value-based services and applications in a secure environment and effectively help to establish an ecosystem tailored towards specific use cases serving the broader ecosystem.
“A good analogy, or maybe a dangerous analogy but one that helps people understand what Marketplace is,” Swan explains, “is to think about it like the iPhone and app store.”
This means that partners via the Work With Trackunit Partnership are afforded the opportunity to go into Trackunit’s software ecosystem and develop apps for the market that address very specific problems. The apps then get launched and any Trackunit customer is allowed to utilize them.
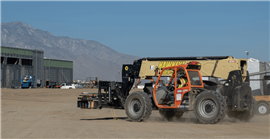
“We have this crazy base of connected machines, more than 1.5 million units are now connected,” Swan says. “And now we can have companies that are industry ecosystem partners, like ERPs and third-party integrators, who are developing apps to solve problems.”
“Marketplace leverages all the security, scalability, domain modelling and data access that Iris provides to generate value that will have real, tangible benefit for customers throughout the value chain,” adds Ullerup. “It’s transformational because it recognizes that construction is digitizing at a speed that single-focused solutions cannot keep up with if we are to serve the needs of every player in the industry.”
While Swan notes how important it is to solve industry problems, he also says collaboration between customers is key. “No one knows industry problems as well as our customers do,” he says. “And we can only do so much, especially for an industry like construction.”
Swan says aerials and access equipment provide a perfect example as to why this technology is needed – and wanted.
“They’re really kind of separate from a lot of the different machine types [on jobsites,]” he says. “As is measuring their productivity and what they do and what they need to do. You can’t compare them to excavators or more traditional models of construction productivity.”
No two sites are alike
Looking at construction work and jobsites, Swan notes how vastly different each project can be.
“There are very well-structured jobs like big condo builds or massive building sites,” he explains. “And then you have little projects that are wedged into tiny corners of cities or rural areas. If you were to go to every construction company and every rental company and every OEM and say, ‘What problem do you want to solve?’ You get a crazy-broad set of what the ‘most important problem’ is.”
And despite Trackunit priding itself on its ability to solve many core problems, “we can’t solve all problems,” Swan says. “But through Marketplace, we’re really opening up this foundation and platform for the entire industry to say exactly what problem is most important” while allowing collaboration between developers and OEMs to get to the bottom of the issue – and solve it.
Trackunit admits that by opening up the floor to the many OEMs within Trackunit’s ecosystem, they are creating competition. But, Swan says, OEMs have always, and will always, be competing – especially when it comes to digital products.
“How do they create the best digital product,” he asks rhetorically. “I think Marketplace is the answer to that, because now, as an OEM, I can create an app and I can differentiate my machine and my digital service, but have it nested inside of a mixed fleet environment. So, I’m still making my machine more attractive, I’m making a better experience and a lower cost of ownership and a more productive machine.”
Fine-tuning fleets
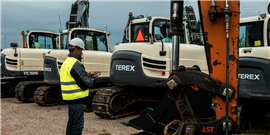
Another major launch occurred during June’s International Rental Exhibition in Maastricht, The Netherlands when Trackunit unveiled its Sites product, a new software geared toward better understanding business operations by automatically detecting jobsites, rental depots and yard.
Through the use of telematics, Sites allows the user to monitor, plan and report based on their sites and allocate machines in its fleet to a specific site.
Other key features include the ability to pinpoint which site the equipment is located at and the ability to monitor the state of the machines.
“For a long time we have been looking at understanding the equipment and how is it operating and how is it being used,” says Ullerup. “Then we looked at data across not just one piece of equipment but the whole fleet. With Sites we are extending that to create a new category in our product suite.
“With the concept of Sites we are essentially making it much easier for the rental industry to see what is on their site or yard, when is equipment coming in or out and where the equipment is.”
Fleet owners and site managers can now leverage live machine data across projects to build site-specific business processes via easy-to-use site dashboards that allow real-time access to all connected machines and equipment.
Auto-grouping, preset alert triggers, and reports generated by a machine’s arrival, departure, and position on a specific site allow users to integrate digital solutions, automate processes, and minimize manual administration of their fleet connectivity on the work site and depot.
“For many of our customers, the focus is not simply on the fleet or individual machines, but rather the sites where work is happening—be that job sites for a contractor, rental depots for a rental equipment manager, or perhaps even a warehouse,” adds Brogaard. “With Sites, fleet managers will be able to apply the power of advanced telematics to what really matters: their unique job sites and depots.”
For rental companies, Sites makes it much easier to see what is on their site or yard, where equipment is and whether it is on its way in or out. For contractors, they will get an up-to-the-minute picture of their job sites eliminating the need for ongoing manual site-level administration.
Fleet owners will also be able to use Trackunit Manager for easier maintenance over time with each site having its own dedicated home page. That will enable the quick identification of problems and instigate remedial action before they become critical and potentially more costly.
Even more debuts
Also on its stand at IRE, the company highlighted its Emissions Reporting app, which enables users to track emissions of machines in real time and keep on top of emission targets.
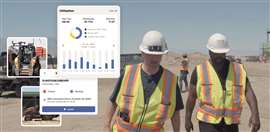
Although currently based on estimated numbers, the app will help companies keep on top of stringent regulatory restraints and monitor, manage and report fleet emissions, according to Trackunit.
The app is designed for both combustion and electric machines and utilizes machine learning and big data to compile a complete documentation of emissions.
Another key launch on its stand was the Data Feeds solution, which allows fleet owners to compile data from OEMs machines and self select the data feeds into their fleet management solution and customize it to their required specification.
This, according to Trackunit, means users can gain machine insights, view and manage equipment and optimize fleet management, as well as several other benefits.
So far, the newly launched solution is connected to machines from 45 OEMs, including Caterpillar, Atlas Copco, Takeuchi, Volvo and Yanmar.
Access Control
In June, Trackunit also produced an outlook for Access Control in Construction, which CEO Brogaard says will increase authorized accessibility, safety and usability, whilst eliminating downtime with on-site equipment.
“If access control can take construction beyond who goes in and out of a job site to deliver real insights on downtime and safety, it will be an industry game changer,” Brogaard says. “We have always had access control. But now that it offers real safety, security and productivity benefits, it is no longer enough to consider it as just the centurion at the door.
“Digitalization over the past two decades and the growth of SaaS-powered businesses has dramatically altered how access control is used in construction. Swipe technologies have been with us since the 1980s but the main game changer over the coming years will be the data-rich insights that are available through ever-more sophisticated telematics devices.”
Brogaard lays out the following five key aspects in the ever-changing construction environment which Trackunit believes will positively drive construction forward.
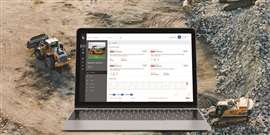
1. Connectivity
There are 359,000 construction equipment operators in U.S. The more connected we become, the more construction as an industry can rely on the quality of the data. That process is dependent on a commitment to data sharing but as the ecosystem evolves, the business sense in data transparency also grows in parallel.
It means connectivity delivers a bundle of benefits that engender a virtuous circle of behavior. Access control is just one of those.
2. Training and education
There has already been steady progress in the correct training and education of MEWP operators, but it varies from company to company, state to state and region to region. Around 200,000 equipment operators annually complete approved training through the International Powered Access Federation (IPAF) which has a worldwide network of over 550 providers, and the training is available in multiple languages.
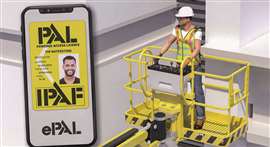
IPAF also offers management training. The challenge for construction in the coming years could be to standardize criteria and access control will play an increasingly important role in that dynamic.
3. Technology
Technology has helped drive the revolution in telemetry over the past few years incubating a data-rich environment that is offering up ever more insights that are actionable and relevant. Analogies with an aircraft’s black box as a conduit for understanding when fatalities occur are no longer far-fetched and could in time, as the industry becomes better at filtering data, catalyze both the downtime and safety agendas.
Approximately 55 percent of construction companies do not exploit the full potential of the data they gather, because 83 percent of these businesses don’t know how to use the data correctly.
4. Safety
IPAF reports that 109 deaths took place on mobile elevated work platforms among member countries in 2022. The real figure is probably much higher when you factor in, for example, earth-moving equipment. Nothing matters more than safety on the job site and access control can play a key role in making that happen. It’s not just about controlling who goes in and out. It’s also about ensuring only those with the right skills go into the most dangerous arenas.
5. Reducing human error
Developments in access control will increasingly eliminate much, if not all, paper reporting out of many on-site processes. It will also gradually help to eliminate the risk of human error. This enables human resources to be used in a more effective and efficient manner, and gradually foster a better workplace.
Circa 33 percent of rental companies estimate that equipment operators do not receive sufficient training to use machines properly, according to a Trackunit study. That will also foster better machine utilization and help the industry in its challenge to manage and eventually eliminate downtime.
“These are steps that companies across construction are implementing, and when included in a systematic program of organizational improvement will drive beneficial outcomes for workers, companies, government and wider society and help raise construction’s profile as an industry to be involved in.”
MAGAZINE
NEWSLETTER
The gold standard in market research
Off-Highway Research offers a library of more than 200 regularly updated reports, providing forensic detail on key aspects of the construction equipment industry.
Our detailed insights and expert analyses are used by over 500 of the world’s largest and most successful suppliers, manufacturers and distributers, to inform their strategic plans and deliver profitable growth.